Traction vs Hydraulic Elevators: Which is Right for You?
- Narendra Sharma
- Nov 22, 2023
- 3 min read
It’s difficult to know what kind of elevator you’re riding unless you’re able to see the mechanics going on behind the scenes.
There are different types of elevators for a reason. Some are better for smaller buildings while others are designed for high-rise transportation. As two of the most common systems used in commercial buildings today, here’s our explanation of traction elevators vs. hydraulic elevators.
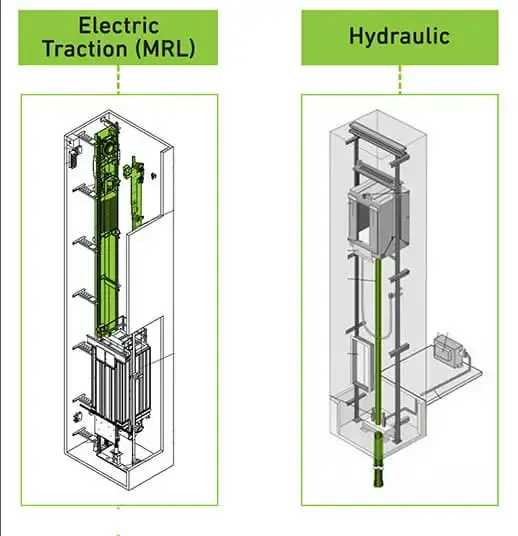
TRACTION ELEVATORS
The major difference between traction and hydraulic elevators is in the way the systems transport the cab. With Traction elevator, the cab is raised and lowered by traction steel ropes or belts on a pulley system. Compared to hydraulic systems, traction elevators:
Uses less energy
Serve mid to high-rise buildings
Ride smoother

Traction elevators use a counterweight to offset the weight of the cab and occupants. With this design, the motor doesn’t have to move as much weight, making it much more energy efficient than hydraulic systems.
Traction elevators are the most common type of elevator. They can be geared or gearless and both model types are driven by alternating current (AC) or direct current (DC) electrical motors.
Geared Elevators
In geared elevators, there is a gearbox attached to the motor that drives the wheel and moves the ropes. Geared machines can reach speeds up to 500 ft./min. These models will have a middle-of-the-road cost in terms of initial investment, maintenance costs and energy consumption.
Gearless Elevators
In gearless traction elevators, the sheave is attached directly to the end of the motor. These models can reach speeds up to 2,000 ft./min. These models have a high initial cost investment and average maintenance costs. They are, however, more energy efficient than geared traction elevators.
HYDRAULIC ELEVATORS
Unlike traction systems, hydraulic elevator don’t use overhead hoisting machinery. Instead, these elevators lift a cab by using a fluid-driven piston that is mounted inside of a cylinder. The necessary fluid has traditionally been oil-based but can be replaced with vegetable oil to decrease the environmental impact.

Compared to traction elevators, hydraulic systems are:
More affordable to install
Less expensive to maintain and repair
Better for transporting heavy loads
Intended for low-rise applications
Hydraulic elevators are most often found in buildings that serve up to five stories because they operate at slower speeds than other types of elevators — typically 150 ft./min. or less.
Another reason for their height limitations is that it takes a lot of energy to raise an elevator cab several stories. To reach high floors with a hydraulic elevator, you would need a longer cylinder and piston.
There are two different types of hydraulic elevators:
Holed The holed type of hydraulic elevator has the hydraulic cylinders placed inside of a drilled hole and allows up to 60’ of travel.
Hole less Hole less hydraulic elevators don’t require a drilled hole, making this type of elevator ideal for existing buildings or in areas where drilling would be too difficult or expensive. Hole-less elevators shouldn’t be installed anywhere that requires more than 40’ of travel.

PROS & CONS OF EACH
Here’s a list of pros and cons for both types of elevators to give you a better understanding of your options.
Hydraulic Elevators
Pros:
Quickest to install
Least expensive to install and maintain
Capable of moving increased weights (i.e. custom cabs)
Lower pit and overhead requirements with standard travel
No crane/roof access required
Above-ground models available with or without machine rooms (pre-engineered only)
Cons:
Limited to low and mid-rise buildings
Machine room required for in-ground applications (viewed as a PRO when service is needed)
Larger power requirements
150 ft./min. max up-speed
Self-Supported MRL (Most Common Traction Elevator)
Pros:
Net travel above 60’
Smaller control room requirements
Smaller motor size
Possibly a quieter ride
Cons:
More expensive to install and maintain
Crane is typically required (building roof cannot be installed over hoistway)
Limited on cab weights
Limited on cab capacities
Increased overhead/pit requirements
4-6 weeks added to project schedule
Comments